Integrated Fermentation Platform
Rational development and scale-up of microbial fermentation processes are challenging as different environmental conditions impact cell physiology, which in turn affect key process parameters such as product titre, rate, and yield (TRY). The Integrated Fermentation Platform (iFP) of the Biofoundry, aims at rapid development of robust bioprocess (from TRL 1 – TRL 3/4 ) by understanding the scale-dependent, environment specific insight of microbial cell factories.
The iFP team approaches the challenge of developing robust bioprocess by integrating bioprocess development with the top-down systems biology methods. Metabolic engineering targets are identified from the observed metabolic and regulatory response of cell factories, thereby enabling engineering a strain towards a stable/robust production strain together with the Biofoundry-Design/Build teams. Overall, the iFP of Biofoundry addresses the significance of integrating the three areas, i.e. (a) Biological engineering, (b) Bioprocess engineering and (c) Biological understanding for the development and design of advanced microbial cell factories.
Starting with the end-in-mind, the iFP team applies theoretical bioprocess design principles to design robust high cell density process. Quantitative methods are applied in the workflow to elucidate strain physiology from different cultivation scale/setup (µL- mL scale with BioLector, Kuhner TOM shaker; mL – L scale with AMBR250® and novel custom designed scale-down bioreactors). Bioprocess data variables (i.e., the cellular phenotype) of microbial cell factories are integrated with appropriate multi-omic data (metallome, transcriptome, proteome, and metabolome) to identify environment specific challenges for production strain and re-design process accordingly.
Further, microbial/industrial robustness of the engineered cell factories are tested in novel scale-down bioreactors where industrial-scale heterogenous conditions are mimicked and robustness of production strains are assessed. All data collected from different cultivation setup are logged based on FAIR principles in LIMS system (Benchling). The online & offline bioprocess data are integrated and analysed using the PAS-X Savvy software (advanced bioprocess data analytical software from Koerber Pharma).
Technologies
- Automated mini-bioreactor platform (AMBR250®, RoboLector)
- Multi-compartmented single-vessel scale-down bioreactors
- Rapid sampling devices
- Protocols for quantitative strain physiology assessment
- Small-scale high-throughput screening & physiological characterization
- High cell density cultivation protocols for prokaryotes and eukaryotes in AMBR250® and other reactors
- Rapid sampling, quenching and extraction for metabolome analysis
- Sampling for transcriptome, proteome and metallome analysis
Example Work
- PhD thesis: Kerssemakers AAJ., Understanding and overcoming physiological stress responses in Yarrowia lipolytica to dissolved O2 and CO2 in fermentation processes.
- PhD thesis: Bafna-Rührer J., Strategies and tools to select E. coli fermenterphiles for industrial application.
Selected Publications
- WO2022/038269A1: Methods, assembly and system for high-throughput, parallel, monitoring of reaction systems.
- Kerssemakers AAK., Øzmerih S., Sin G., Sudarsan S., Dynamic interplay between O2 availability, growth rates and the transcriptome of Yarrowia lipolytica, Fermentation 2023 9, 74.
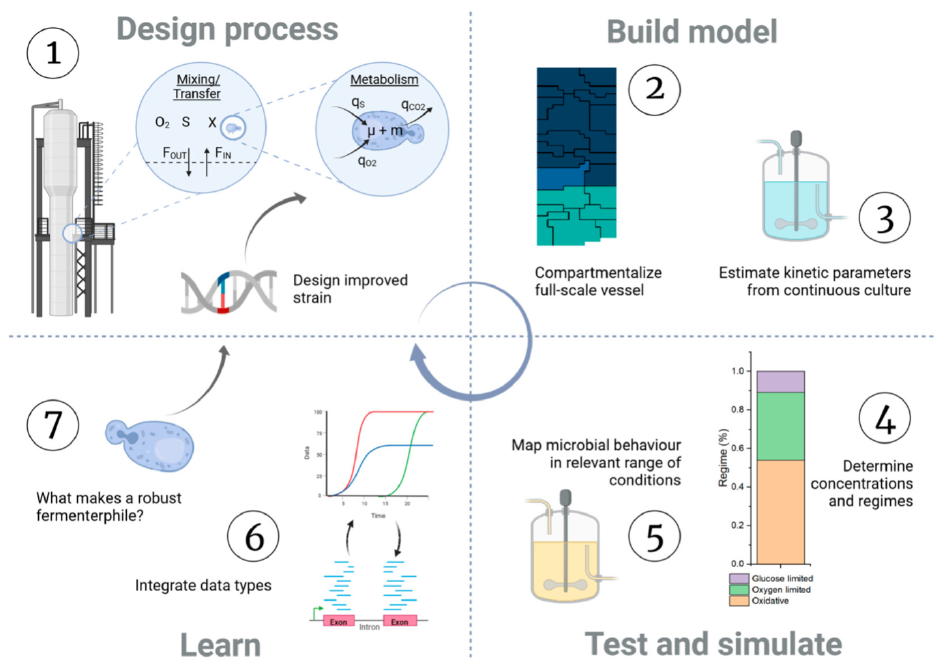
Contact
Suresh Sudarsan Head of Integrated Fermentation Platform sursud@biosustain.dtu.dk